Casting model
Model for cast iron component
To produce cast iron, we need a model that can leave an imprint in sand, which can then be filled with approximately 1,500 degrees hot iron. A model can be made in any shape-stable material depending on complexity, tolerances, and the number of castings to be made. It can be made of wood, plastic, aluminum, iron, or even styrofoam if the model only needs to be used once. We help you find the perfect model material for your casting.
The casting model reflects the geometry of the component. The model is divided into two and is always about 1% larger than the desired component because cast iron shrinks by 1% during solidification/cooling (depending on geometry and alloy).
If there needs to be a cavity in the component, a core box must also be made to form the sand core. The core is placed in the casting model to create the cavity or a hidden contour in the final component.
Cast iron prototypes
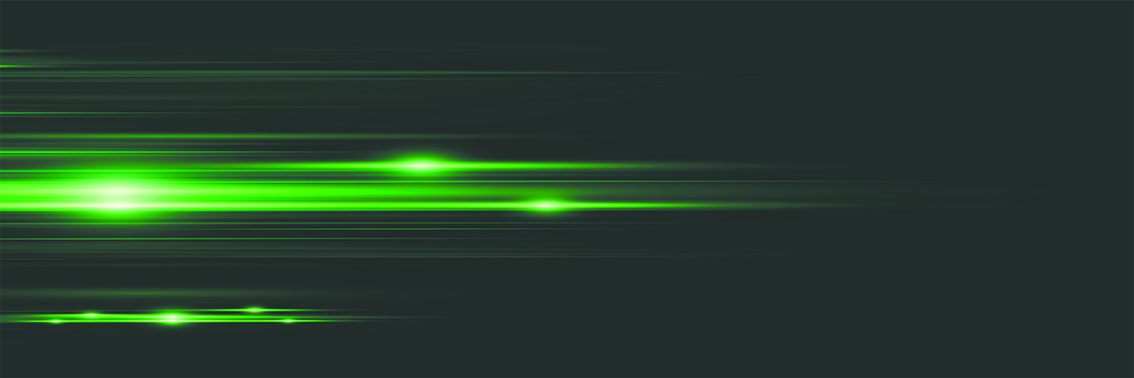
"Time to market" is more crucial than ever. We offer existing customers our "Rapid Prototyping", where we can offer delivery including standard casting models within 2-4 weeks - at ULDALL we call this "Fast Lane Prototyping".
The difference between "Fast Lane Prototyping" and 3D printing technology or disposable models is that, even after the prototype phase, we can produce x number of items with the casting model.
We offer our complete range of irons (55 alloys) and offer from one to 20 pieces within the time frame. Even extensive quality control carried out in our own laboratory can be carried out.
This is possible as we have our own PTA department for design and simulation (MAGMASOFT)® with backup from our parent company, BIRN, during periods of pressure. We have strong and long-standing relationships with our local model carpenters. Most important of all, however, are our 55 skilled "Real Ironmen" who handle our "Fast Lane Prototyping".
3D printed molds
Today, there are 3D printers that can print a mold or core in sand, thereby eliminating the need for a model.
However, this is still a very costly process, which is therefore primarily used for prototypes.
CONTACT
"Time to market" is more crucial than ever. We offer existing customers delivery of prototypes including standard casting models within 2-4 weeks.
Dion Brun, Sales Director
Contact us